📅 Timeline: Q2 2023 – Q3 2023
💰 Budget: USD 20,000
🎯 Objective: Upgrade obsolete equipment to reduce maintenance costs and improve operational efficiency.
Situation:
Aging equipment in the Asphalt Enamel Plant led to high maintenance costs and operational inefficiencies, necessitating a refurbishment project to restore functionality and enhance reliability.
Task:
🔍 Assess outdated machinery and identify critical refurbishment needs.
🔧 Overhaul and upgrade components to extend equipment lifespan.
💰 Optimize budget to achieve cost savings without full replacement.
Action:
🛠 Reverse Engineering & 3D Drawing – Redesigned key equipment (Indexer).
🔄 Component Replacement & System Upgrades – Enhanced performance with modernized parts.
📊 Budget-Controlled Execution – Ensured cost-effective implementation within USD 20,000.
Result:
✅ Reduced Maintenance Costs – Lowered repair frequency and expenses.
🚀 Improved Reliability – Enhanced equipment performance and longevity.
📉 Minimized Downtime – Smoother operations and increased efficiency.
💰 On-Time & Within Budget – Successfully refurbished without financial overruns.
This strategic refurbishment optimized plant operations, ensuring long-term cost efficiency and reliability. 🔧🏭
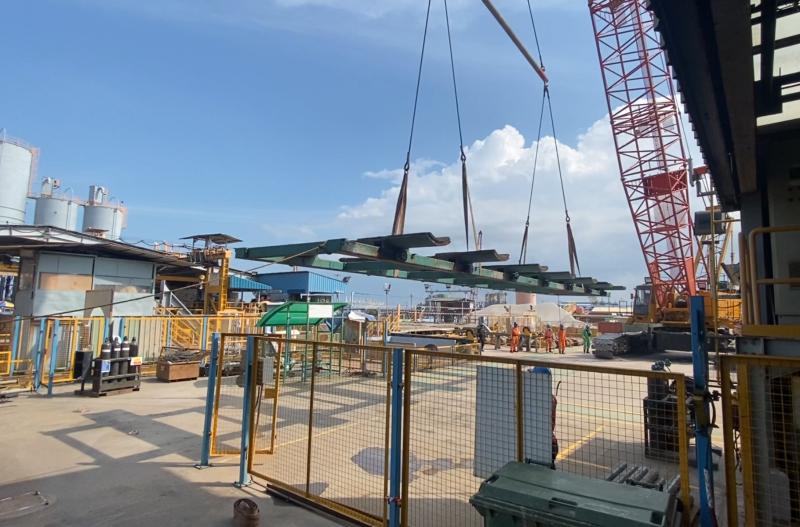
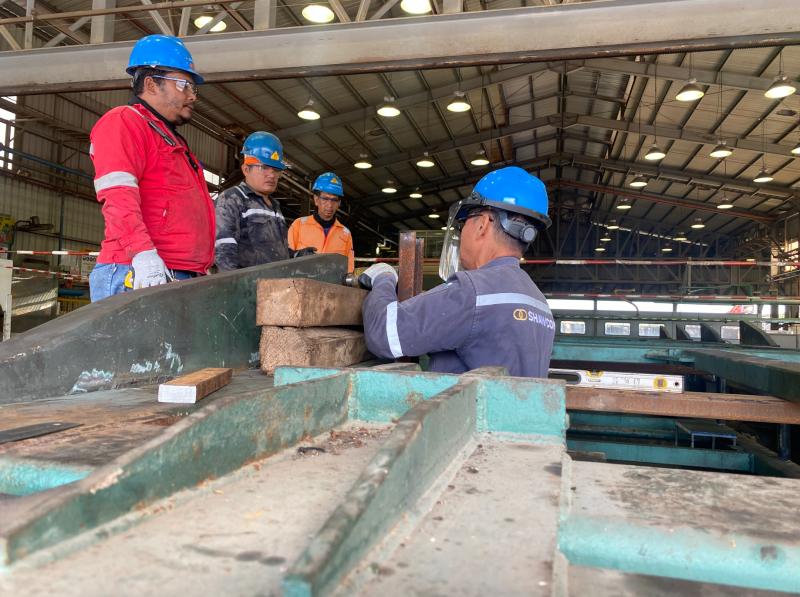
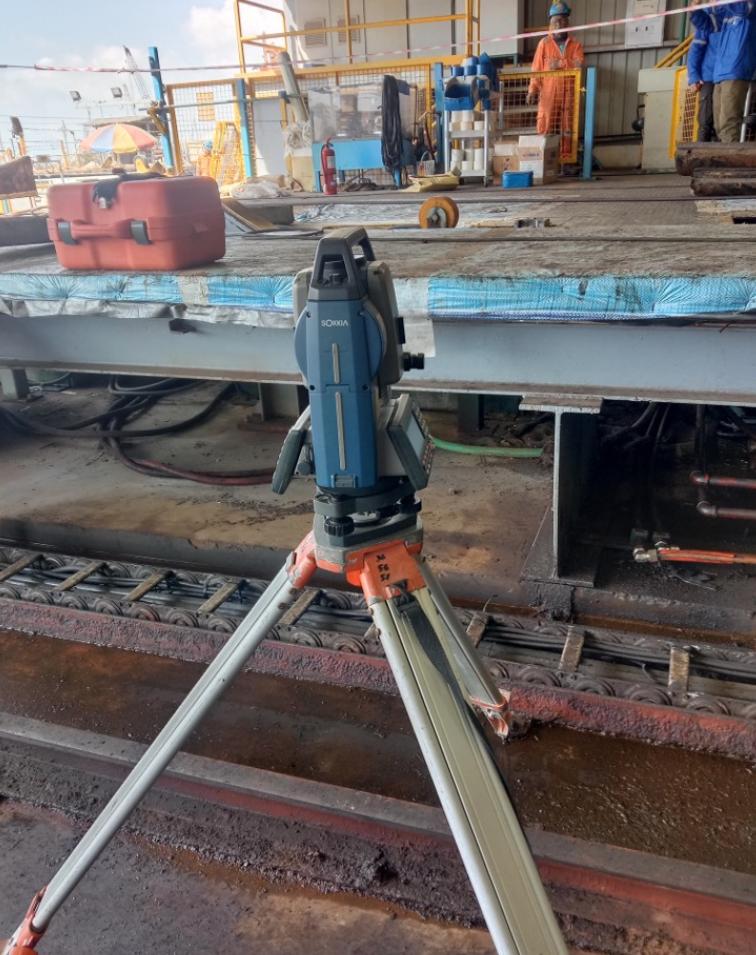
Below is the documentation of the Refurbish activities, with below is the Reversed Engineering of 3D Drawing of Indexer Equipment (MI).
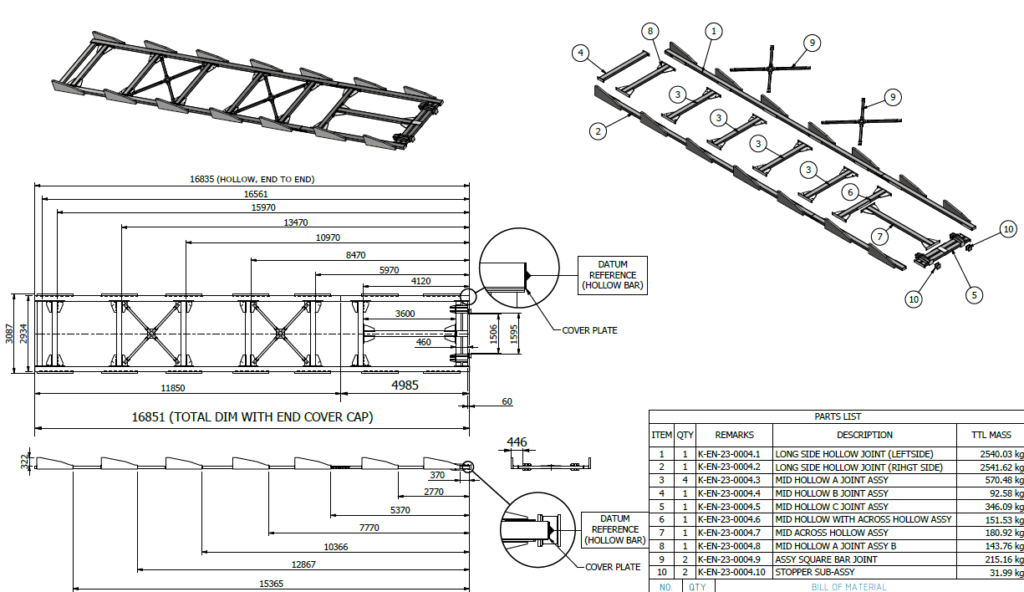
Click to see Project details
📅 Project Timeline: Q2 2023 – Q3 2023
💰 Project Budget: USD 20,000
🎯 Objective: Refurbish outdated equipment to reduce maintenance costs and enhance operational efficiency.
Objective:
This CAPEX project focused on refurbishing aging equipment at the Asphalt Enamel Plant to address high maintenance costs and operational inefficiencies. By overhauling and upgrading key machinery, the project aimed to restore performance, extend equipment lifespan, and optimize production reliability.
Rather than a full replacement, this cost-effective refurbishment ensured maximum efficiency while staying within budget.
Refurbishment & Equipment Upgrade:
Key engineering improvements included:
🔍 Machinery Assessment & Reverse Engineering – Identified outdated components and developed 3D models for Indexer Equipment.
🔧 Component Replacement & System Upgrades – Installed modernized parts to enhance durability and performance.
🛠 Operational Optimization – Improved functionality while ensuring seamless integration into the production process.
📊 Inspection & Performance Testing – Verified reliability, efficiency, and compliance with operational standards.
💰 Budget Optimization – Managed procurement and execution within USD 20,000.
By focusing on refurbishment rather than full replacement, the project delivered substantial cost savings while achieving performance improvements.
Operational Impact & Benefits:
🚀 Reduced Maintenance Costs – Lowered repair frequency and extended equipment lifespan.
✅ Enhanced Reliability & Performance – Improved plant efficiency and operational stability.
📉 Minimized Downtime – Ensured smooth transition back to full production capacity.
📈 Cost-Effective Modernization – Achieved long-term savings while staying within budget.
Budget Management & Execution Strategy:
💰 Efficient Resource Allocation – Selected cost-effective, high-quality materials.
🛠 Strategic Engineering Approach – Minimized operational disruptions with phased execution.
📊 Rigorous Testing & Quality Control – Ensured optimal performance before commissioning.
With no budget overruns, the project successfully enhanced plant operations while maintaining financial discipline.
Conclusion:
The Asphalt Enamel Plant Refurbishment project delivered a modernized, reliable, and cost-efficient system, reducing maintenance costs and enhancing production stability. This CAPEX initiative underscores our commitment to continuous improvement and operational excellence. 🔧🏭