π
Project Timeline: Q1 2024 β Q3 2025
π° Project Value: USD 3.5 Million
π― Objective: Upgrade the 3LPP/E and MLPP plants to increase capacity, enhance efficiency, and meet client specifications while optimizing material handling and production throughput.
π· Situation:
The 3LPP/E and MLPP plants required upgrades to increase production capacity, enhance efficiency, and align with future client requirements. Existing infrastructure limited throughput and flexibility, creating operational inefficiencies. To address these issues, a CAPEX investment was initiated to modernize equipment, improve material handling, and expand plant infrastructure.
π· Task:
πΉ Enhance material throughput with new extrusion and drying systems.
πΉ Improve plant efficiency through optimized dosing, weighing, and storage solutions.
πΉ Expand building infrastructure to accommodate new equipment and process enhancements.
πΉ Ensure compliance with client-specific requirements and quality standards.
πΉ Optimize plant layout using 3D visualization and simulations for the best fit.
π· Action:
β
New PS Screw Installation β Upgraded MLPP plant for higher polystyrene processing capacity.
β
3LPP/E to 3LPS Conversion β Enhanced extrusion and material handling systems.
β
New Dehumidifying Dryers β Installed high-capacity dryers (3L: 1100 kg/hr, MLPP: 2400 kg/hr) to ensure material quality.
β
Advanced Dosing & Weighing System β Improved material accuracy and reduced waste.
β
Silo Installations β Added three new silos (two 5mΒ³ silos + 10mΒ³ silos for MLPP, one 5mΒ³ silo for 3L).
β
Building Expansions β Structural modifications for equipment accommodation & process optimization.
π· Result:
β Increased Production Throughput β Upgraded extrusion systems boosted capacity to 2400 kg/hr, reducing processing time.
β Enhanced Operational Efficiency β Optimized material handling, drying, and dosing systems minimized downtime.
β Improved Client-Specific Compliance β Tailored upgrades ensured seamless project execution per client demands.
β Future-Ready Plant β The expansion and equipment upgrades positioned the facility for long-term scalability.
β Optimized Workflow β 3D visualization streamlined layout decisions, ensuring a perfect plant fit.
This CAPEX initiative strategically strengthens the plantβs capabilities, ensuring higher efficiency, cost savings, and production reliability for future demands. π
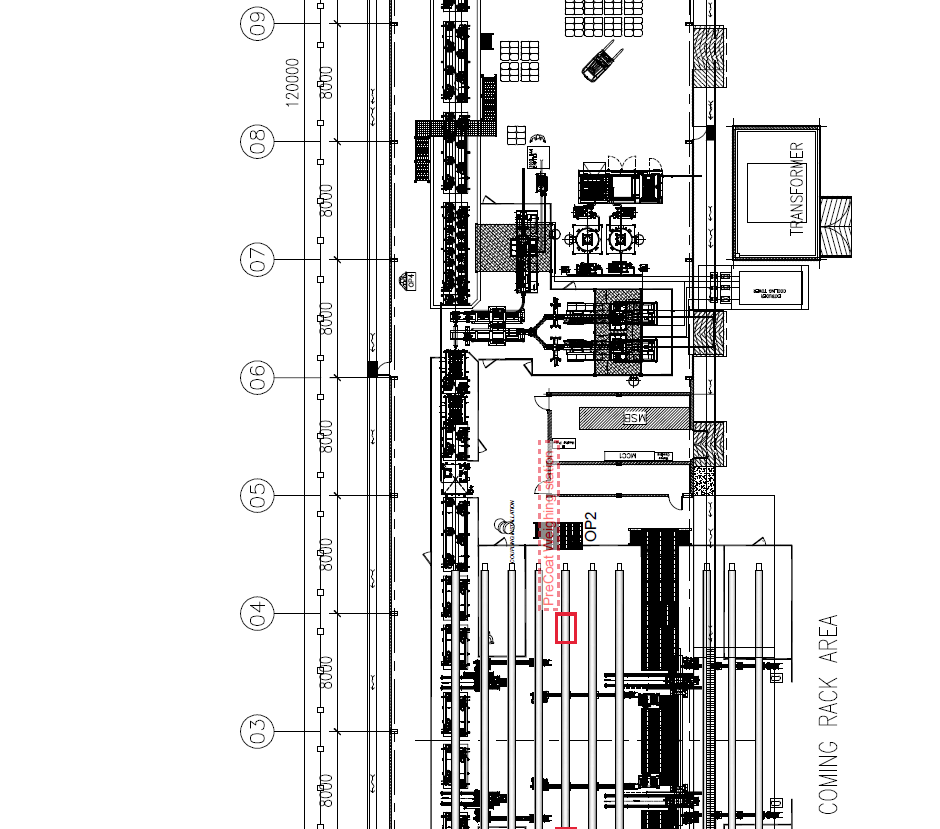
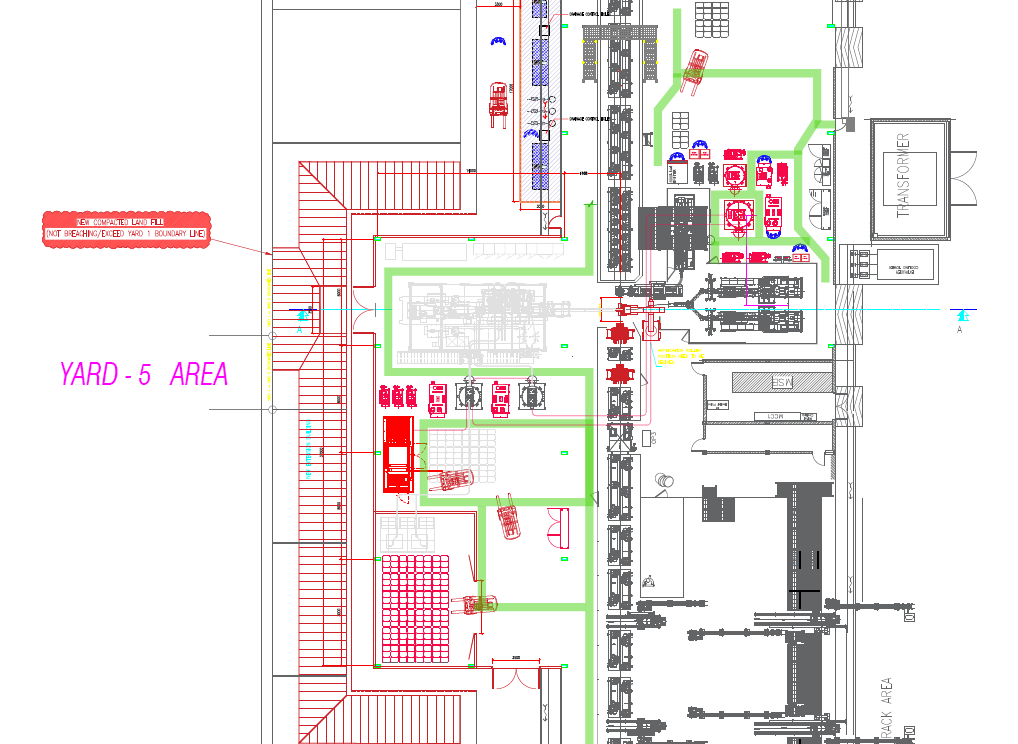
To simplify the presentation for top management, I created a 3D visualization for better clarity and understanding.
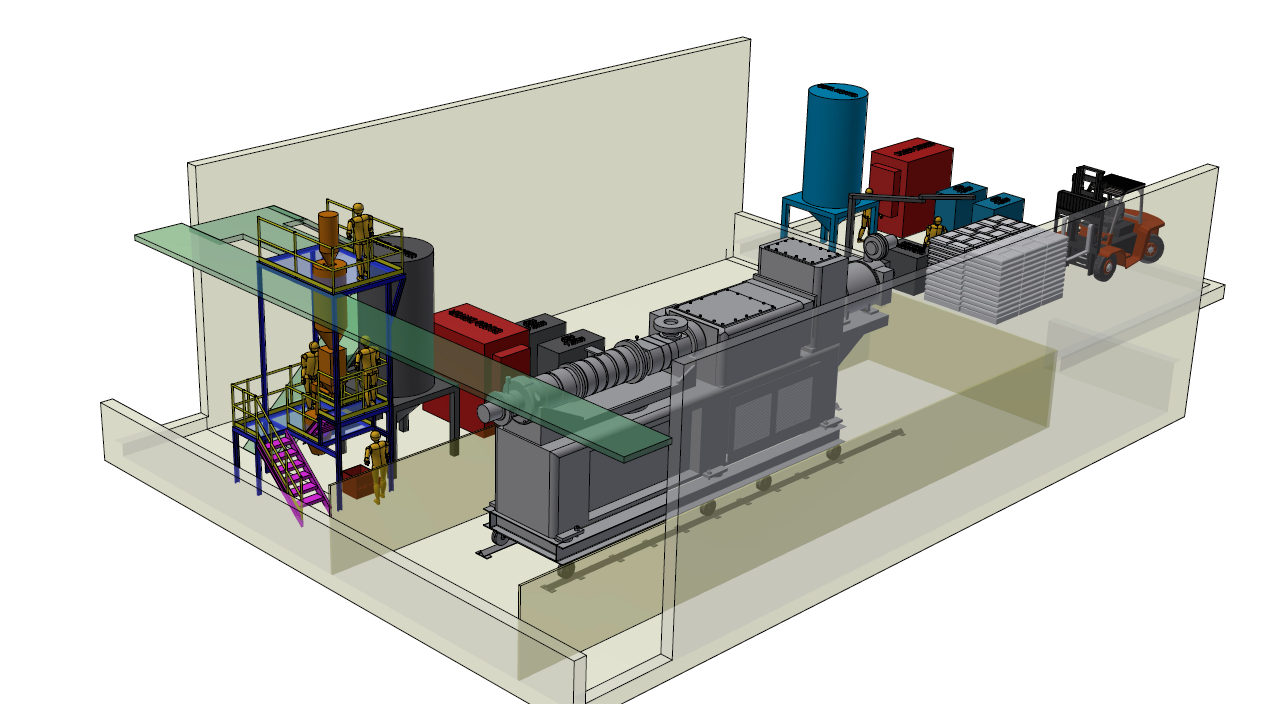
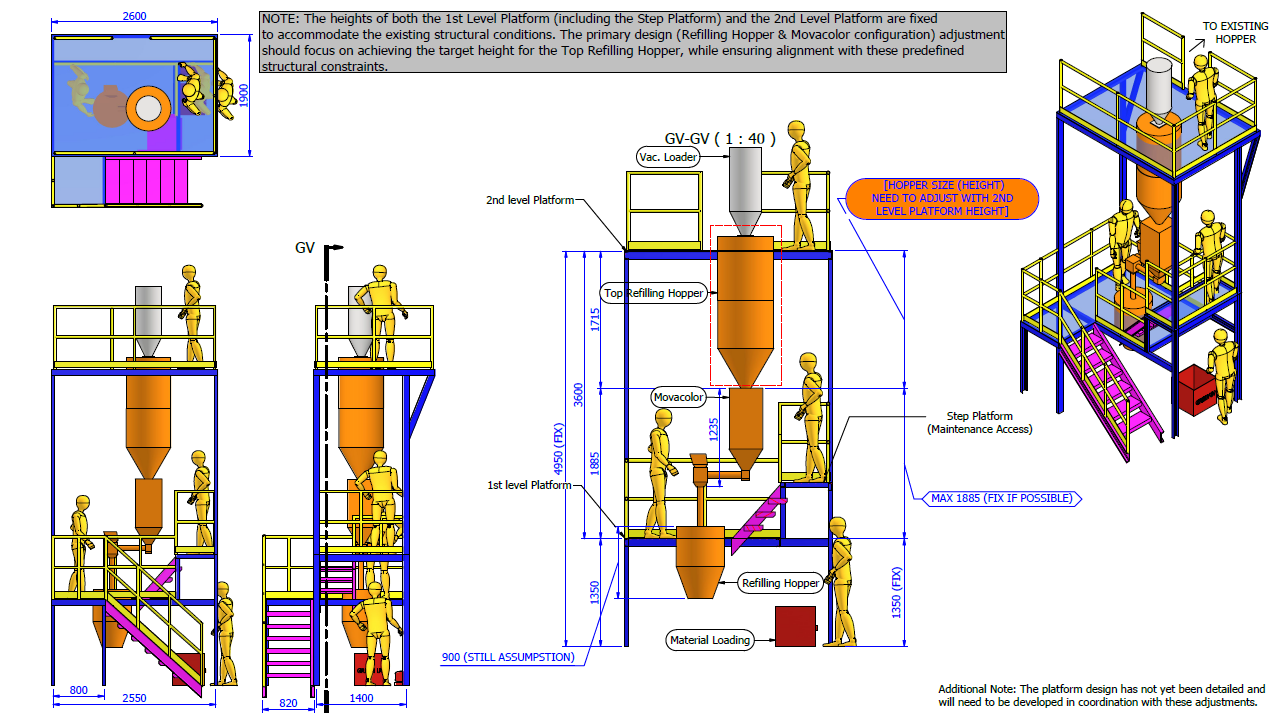
To select the best option, I conducted a study of several potential layouts to ensure the optimal fit for the project. As below:
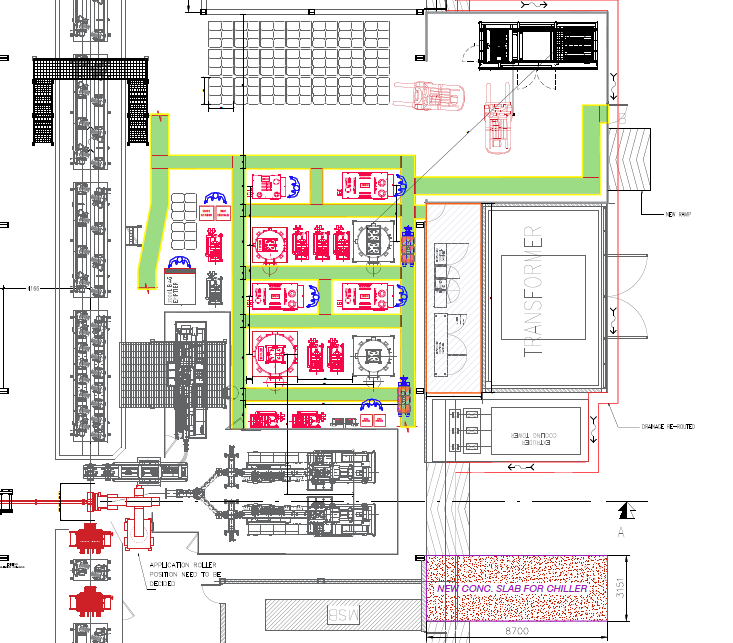
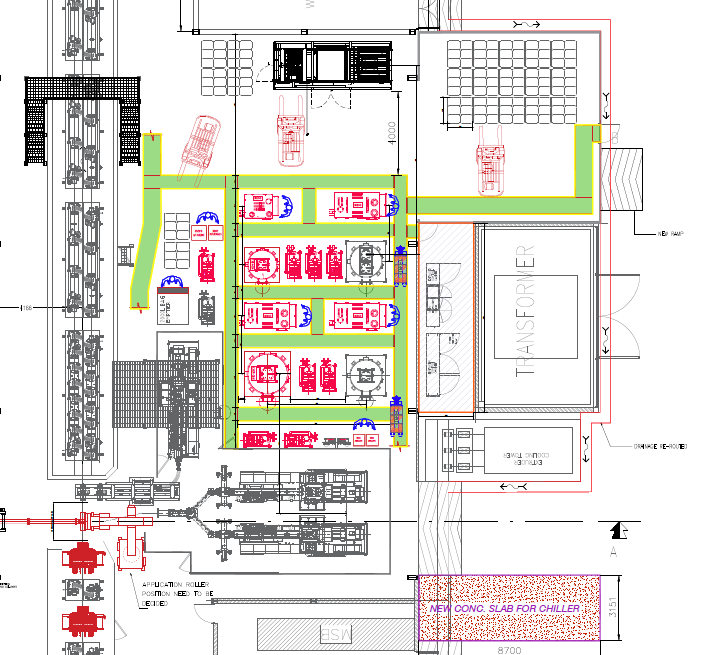
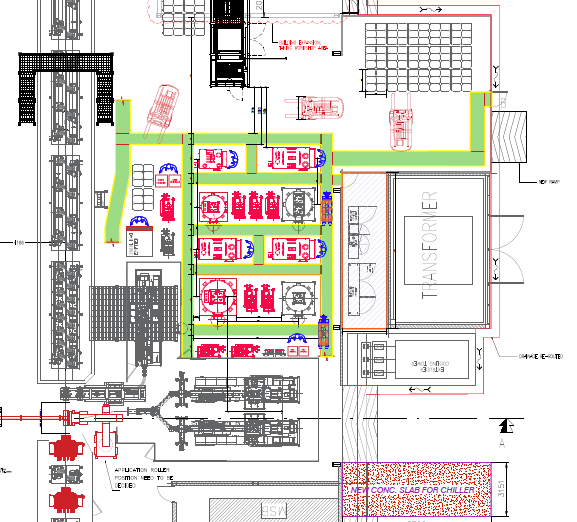
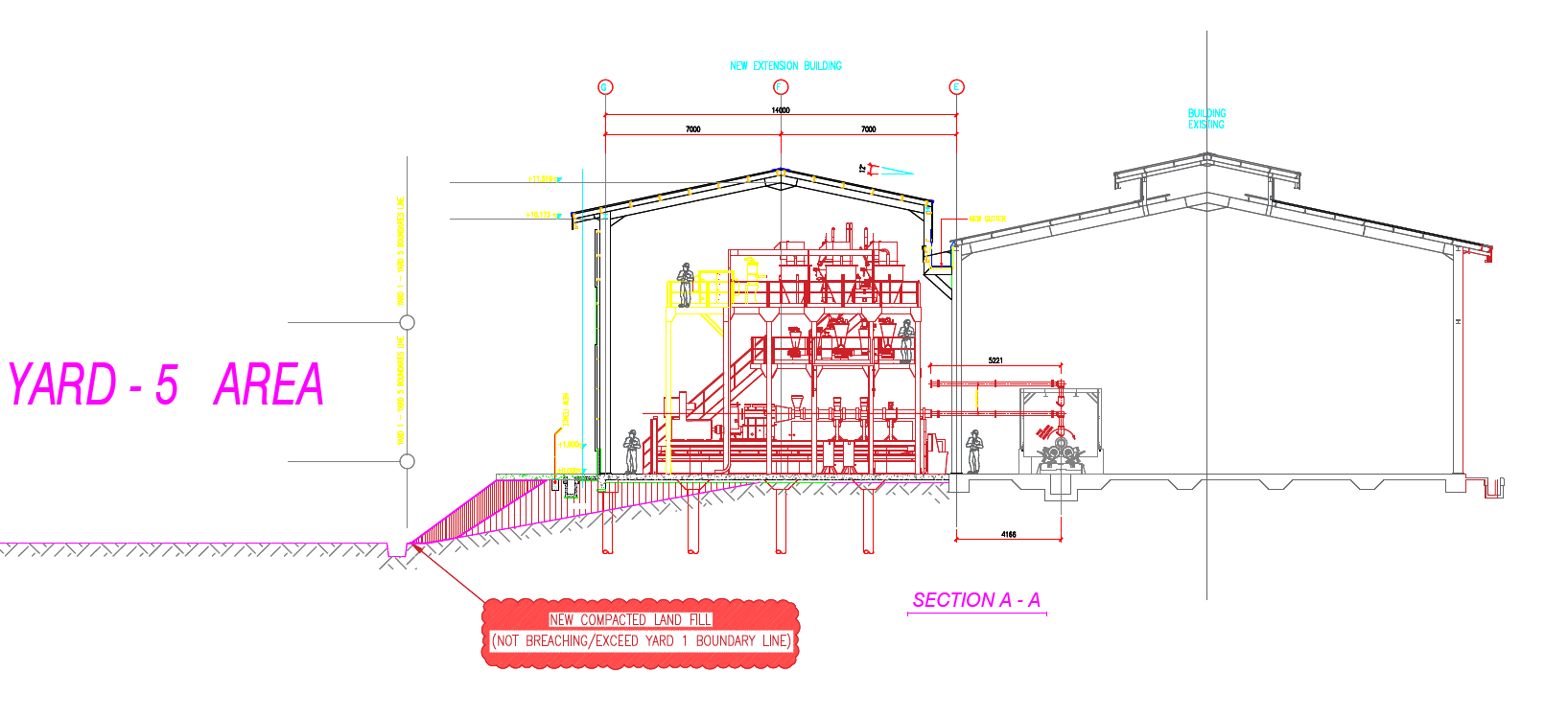
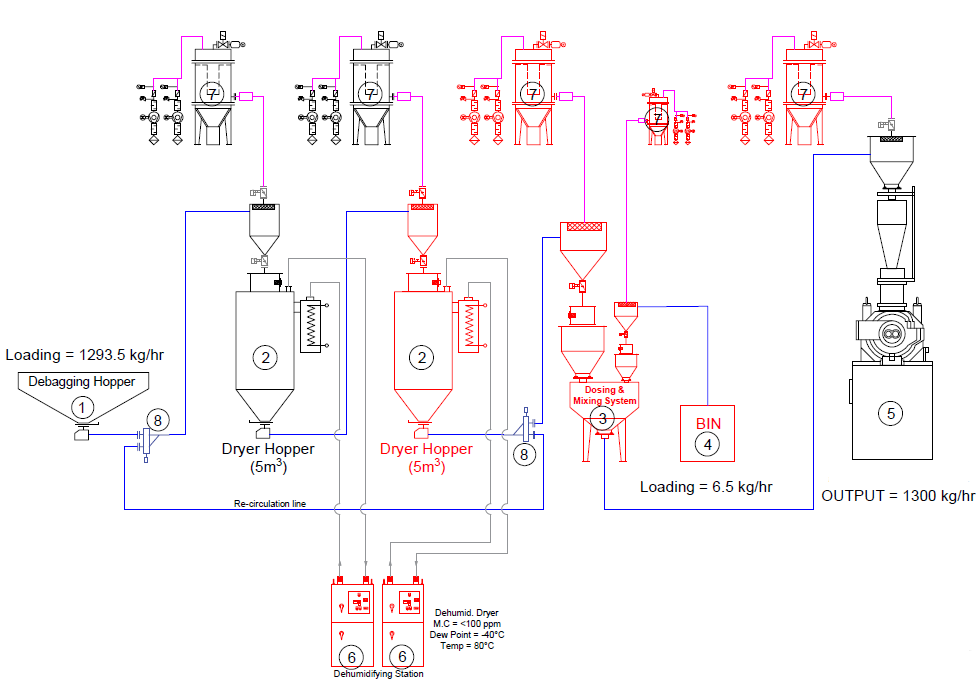
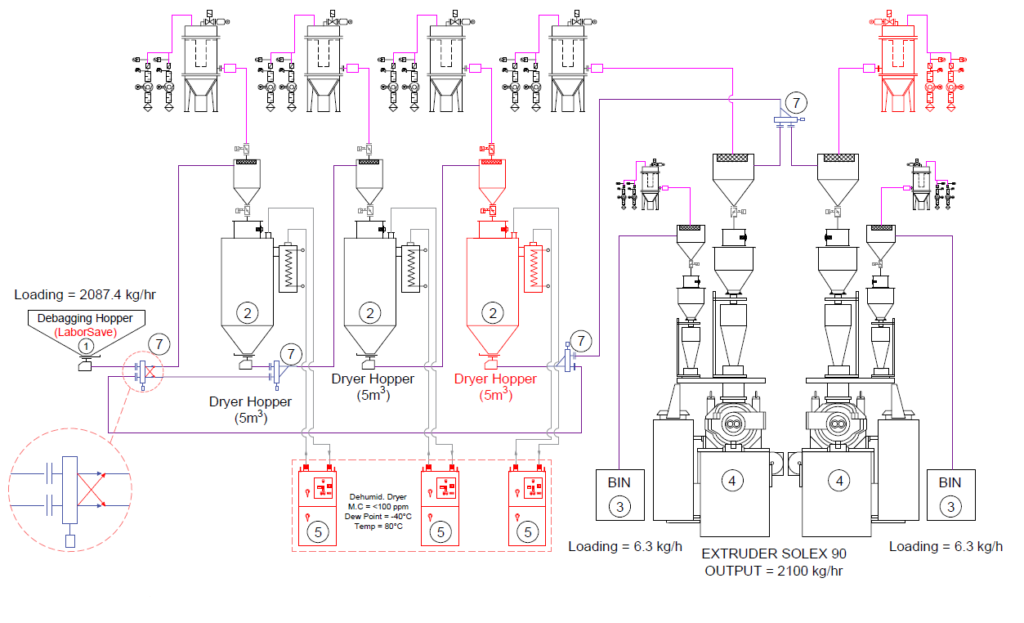
To ensure the layout perfectly fits our plant, I conducted a detailed simulation.
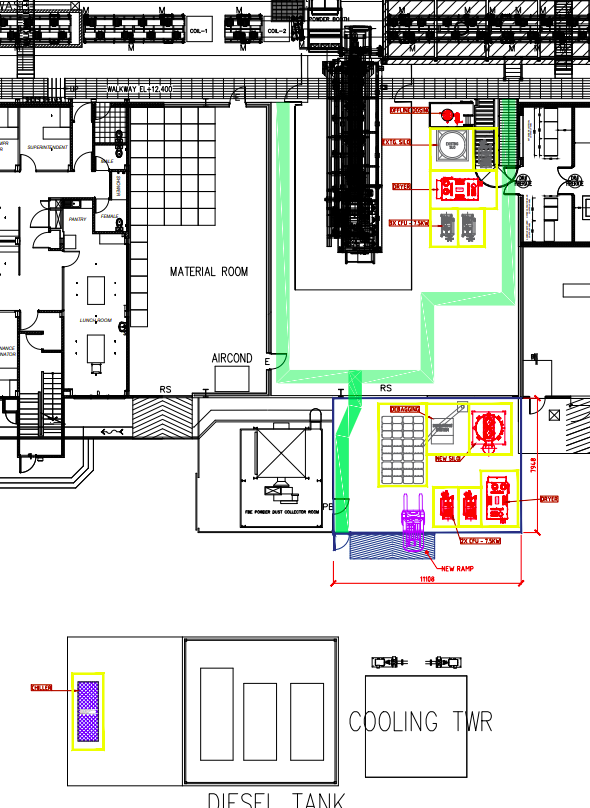
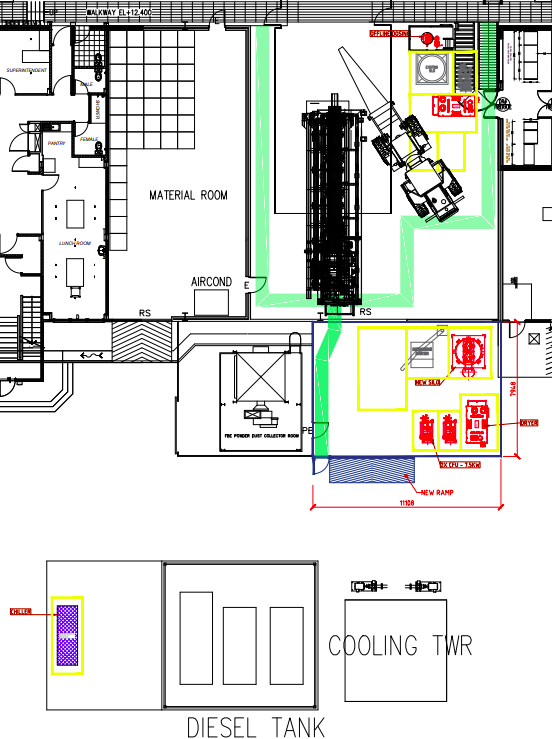
Click to see Project details
π
Project Timeline: Q1 2024 β Q3 2025
π° Project Value: USD 3.5 Million
π― Objective: Upgrade the 3LPP/E & MLPP plants to enhance production capacity, increase efficiency, and meet specific client requirements.
πΉ Background & Objectives
The 3LPP/E and MLPP plants required significant upgrades to meet evolving industry demands and client specifications. This CAPEX project was initiated to:
β
Increase Production Throughput β Enhance extrusion and material handling capacity.
β
Optimize Material Processing β Improve drying and dosing accuracy to reduce waste.
β
Enhance Infrastructure β Expand facilities to accommodate new equipment.
β
Ensure Future Readiness β Upgrade systems for long-term scalability and operational resilience.
To facilitate decision-making for top management, a 3D visualization was developed for a clear and concise presentation. Multiple layout options were evaluated through detailed simulations to determine the most optimal configuration.
πΉ Project Scope & Implementation
1οΈβ£ Process & Layout Optimization
π Engineering Study β Conducted comprehensive layout simulations to identify the best plant configuration.
π Capacity Analysis β Assessed existing production constraints to maximize efficiency.
π Structural Modifications β Expanded infrastructure to integrate new equipment seamlessly.
2οΈβ£ Equipment & System Upgrades
π§ New PS Screw for MLPP Plant β Installed to increase material throughput and optimize polystyrene processing.
π 3LPP/E to 3LPS Conversion β Upgraded extruder and material handling systems for higher efficiency.
π₯ New Dehumidifying Dryers β Installed high-capacity drying systems:
- 3L Plant: 1100 kg/hr
- MLPP Plant: 2400 kg/hr
β Dosing & Weighing System β Implemented an advanced system for precise material measurement and waste reduction.
π Silo Installations β Added: - Two 5mΒ³ silos + 10mΒ³ silos for MLPP
- One 5mΒ³ silo for 3L
π Building Expansions β Expanded facilities to house new systems.
3οΈβ£ Performance Monitoring & Quality Control
π‘ Real-Time Monitoring β Implemented systems to track process stability and material quality.
π Validation Testing β Conducted drying efficiency tests, extrusion trials, and material integrity checks.
β
Regulatory Compliance β Ensured all installations meet industry standards and client specifications.
πΉ Key Benefits
β
Increased Throughput β Boosted extrusion capacity to 2400 kg/hr, significantly reducing production time.
β
Operational Efficiency β Optimized material handling, reducing downtime and enhancing workflow.
β
Enhanced Product Quality β Improved material drying & dosing accuracy, ensuring consistent output.
β
Scalability for Future Expansion β Infrastructure upgrades allow for seamless adaptation to future demands.
β
Cost Savings & Process Optimization β Reduced waste, minimized defects, and improved material utilization.
πΉ Budget Management & Execution Strategy
π° Strategic Procurement β Sourced high-quality equipment at optimized costs.
π Efficient Installation Planning β Minimized downtime by aligning with plant operations.
π Rigorous Quality Control β Ensured all components met performance & safety benchmarks.
πΉ Future Expansion & Scalability
π Additional Throughput Enhancements β Upgrades planned for further increasing production capacity.
π Further Infrastructure Development β Continued facility improvements for long-term growth.
πΉ Conclusion
The 3LPP/E & MLPP Plant Upgrade CAPEX Project is a strategic initiative that enhances production efficiency, ensures future scalability, and meets client requirements. With new extrusion systems, advanced material handling solutions, and infrastructure expansion, this project optimizes manufacturing performance while ensuring cost-effectiveness and regulatory compliance.
π This initiative positions the facility for long-term operational excellence and sustained industry leadership. π